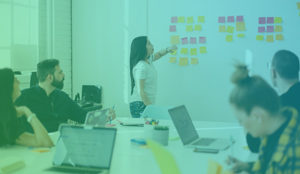
5 Key technologies that can speed up your product development life cycle
In one of our previous posts, we mentioned how product development can be an extremely tedious process that requires a lot of iterations and redesigning. It is for this very reason why DVT manufacturing is a crucial step during your product development life cycle…